Sustainable reefer refrigeration: barriers and opportunities
For example:
- The need for ships to burn low sulfur crude oil for main and auxiliary engines, can and will be reduced in the next generation of vessels
- Newer compression and controls technologies are making it more efficient for reefers to draw power from auxiliary engines when shipping refrigerated cargo
In fact, shipping companies and ports have long been running initiatives aimed at advancing their overall green credentials. The success of which even led to suggestions (during the COP26 sustainability summit) that the International Maritime Organization’s overall targets for decarbonization were “unambitious”.
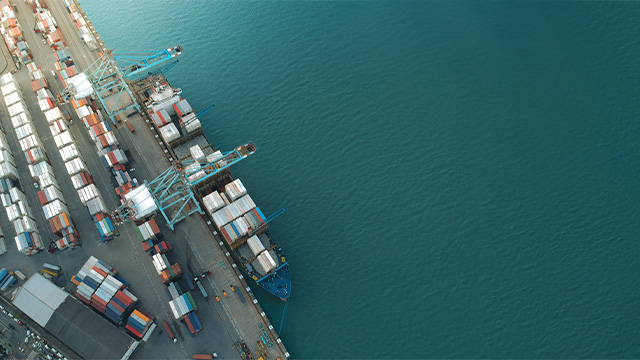
In response, companies are now setting their own targets of being net zero by 2050 – with somecontainer shipping lines looking to achieve this goal ten years earlier than that. These are significant objectives that demand immediate investment in new vessels and reefer containers, and given the timeframe it’s evident a 5-7 year ‘window of opportunity’ for innovation is now open.
Such are the headlines at least, but finding instances of measurable, real-world progress can at times be difficult. Particularly when it comes to reefer sustainability and energy efficiency. A sizeable challenge given the estimated 3.2 million TEU (twenty-foot equivalent units) currently in use.
Refrigerants of choice
Refrigerants have a GPW (Global Warming Potential) level set by the Intergovernmental Panel on Climate Change (www.ipcc.ch) at the UN. Armed with this data it can seem easy to just compare values and select the lowest. But that’s not the whole picture. Other factors also need to be considered, such as:
- The volume charged, and the total unit’s GWP
- Design and component selection, pressures, and system leak rate
- The process for end-of-life recovery
All of which are important concerns when measuring “cradle-to-grave” sustainability. Yet here reefer manufactures can take the lead. For example, Thermo King has for years used a medium pressure refrigerant that has a lower charge but higher GWP per kg. Despite this combination however, the technology delivers a comparable level of impact for refrigerant lifecycle, the best pulldown, and the ability to protect valuable cargo down to -40C.
Progress is certainly being made, and in recent years the industry has developed lower GWP potential refrigerants. Obstacles still exist though in terms of capacity, flammability, availability and cost, that continue to hamper “Marine Reefer” stakeholders as they journey to a more sustainable future:
- From the R-134A and R-452A refrigerants commonly used today, which have global warming potentials (GWPs) of 1300 and 1945 respectively (IPCC AR5 rating)
- To R-513A which has a markedly lower GWP of 573
- With the future goal of running reefers on R-1234yf, with its GWP of just 1
Cause and effect
The first main obstacle relates to infrastructure, in terms of the reefer units available to run alternate refrigerants, operational set-ups with availability trained staff around the world, and the associated inspection capabilities.
- For containers, the simple fact here is not all reefers are designed in the same way to offer the same utility. Which basically means that not all existing investments are easily adapted to deliver the sensors and motors etc. required to run more flammable refrigerants.
- For shipping set-ups, the issue here is one of transition. For example, the move to more sustainable refrigerants will inevitably lead to multiple variants being used across the globe. Yet shipping lines are understandably averse to carrying stores of different refrigerants on their vessels – particularly the more flammable versions. These types of practical restrictions still require an effective, long-term solution.
- For inspection capabilities, these are centered on refrigerants like R-1234yf which are mildly flammable (and come with their own ISO standard 20854). Using them means more routine checks by qualified inspectors, which in turn demands a testing infrastructure be put in place globally – a level of coordination and standardization of workflow that remains a work in progress. In other words, a Pre-Trip Inspection for R-1234yf charged units that includes a full physical inspection and the documenting of results.
Balancing cost and outcomes
Another factor in all of this is cost. That’s because it requires money to run more inspections, to buy new refrigeration units, or modify existing ones. Equally, the next generation of refrigerants also need to deliver the same energy consumption as what’s gone before as a baseline – and ideally deliver noticeable improvements.
Another important dimension to cost, is the price of effective recovery and recycling across the lifetime of a unit. The equation here typically is that the more complexity involved, the more flammable or dangerous the chemicals involved (such as PFAS in R-1234yf), the greater the cost of recycling.
Such concerns are likely hold back investments till 2024-2025. But in truth that’s the date that new sustainability technologies need to be launched to meet IMO deadlines. A fact that highlights the scale of the task, and the need to act as a united marine reefer container industry.
Charting the ideal course
As for playing our part in helping introduce more sustainable refrigerants, Thermo King works to three key objectives: right refrigerant, right energy consumption, right cargo protection.
Our sustainability improvement efforts are designed to have a direct impact via lower GWP refrigerants and each unit’s manufacturing footprint. Equally, they also have an indirect influence through the delivery of lower energy consumption and the avoidance of food loss and waste.
That’s why we continue to innovate in imagining new technologies to give our customers the best of all worlds:
- To optimize energy efficiency, we offer solutions such as CFF, which uses a low-pressure refrigerant to minimize fuel consumption – which makes it 20% more efficient than other units (and equates to $65 in a loss saving for most standard trips of fresh products like bananas, mangos, pineapples,,)
- We also give customers greater control of energy consumption, with features such as an energy logging system which documents energy use for sustainability reporting
- All our units also deliver industry-leading pull-down and cargo protection, while being designed for adaptability – so each can be quickly upgraded for use with alternative refrigerants
This we do to help reduce the cost of sustainability, to minimize the potential for food loss, and to ensure your reefer fleet remains future ready.
Prepare the way for long-term success
Embracing the next generation of sustainable refrigerants for marine reefers is a task that introduces a variety of sizeable challenges. But with Thermo King, we can help you implement a long-term roadmap that delivers immediate benefits for both customers and the bottom line.
You can read more about our portfolio of marine technologies here.
Other relevant articles that might interest you
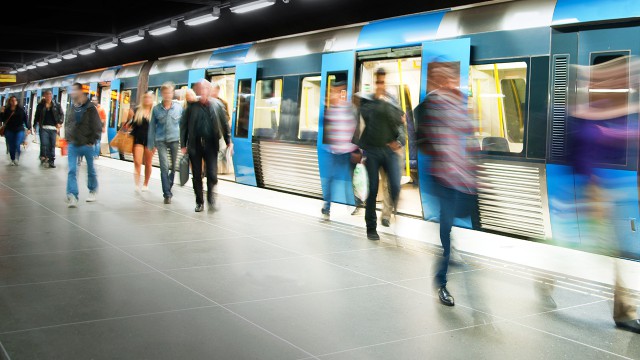
Rail
5 rail megatrends – assessing the industry’s future direction of travel.
It’s no understatement to say there’s a lot of interest in the railway sector …
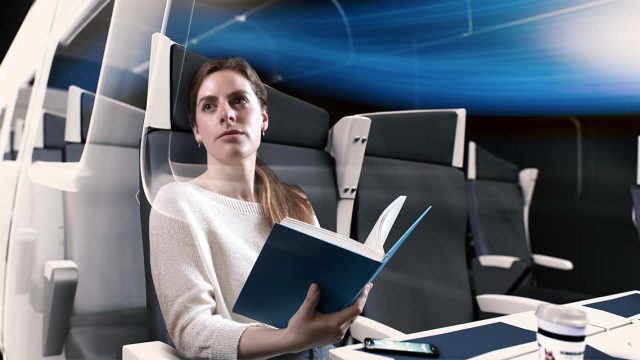
Rail
Our Rail HVAC philosophy.
Heating, ventilation, and air conditioning, also known as HVAC, impacts the …