Putting innovation to the test: Thermo King’s Engineering and Technology Center
Meeting this expectation requires access to a wide array of expert viewpoints, practical analysis, and cutting-edge test facilities. A demand for talent and technology that with Thermo King leads to a state-of-the-art facility in the Czech Republic…
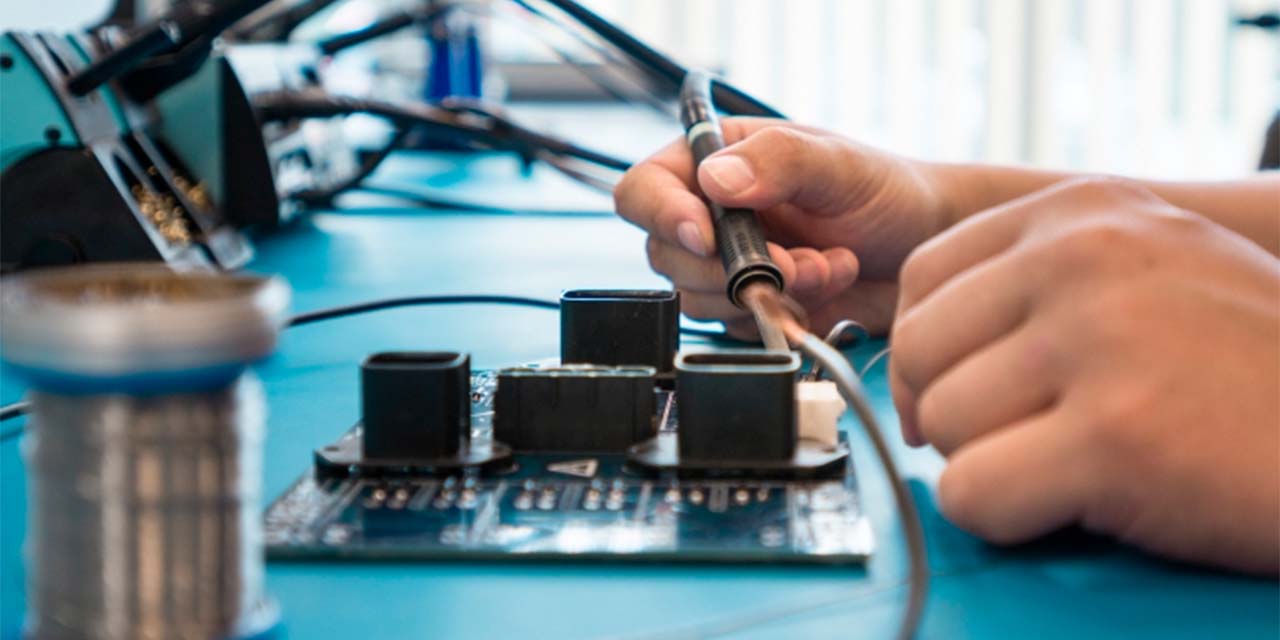
A hub of testing and quality excellence
Located in the town of Hostivice is the Engineering and Technology Centre (ETC) of Prague. It’s a site that has been active since 1948, with the latest facilities constructed in 2007. Home to around 60 specialists, the center’s engineering services are aligned to three primary goals:
- To provide a center of excellence for quality and reliability testing
- To act as a hub for new technology development and design
- To provide a customer demonstration facility of Thermo King products in action
As a result, ETC brings together a unique combination of design and testing capabilities – arranged into four main focus areas:
Electrification testing and R&D
It’s here that the center helps advance Thermo King’s product roadmap for electrification. This is essential work for assessing currently available technologies, and developing new options where none currently exist. The span of work completed is vast, and includes:
- Hardware, software design and testing: covering analog and digital circuit design, schematics and PCB layout design, and embedded systems – as well as rapid prototyping, testing, and validation
- Electromagnetic compatibility testing: which includes electrostatic discharge testing and EMC simulations, accredited to ISO17025 and covering all rail, industrial, and air standards
- Electric motors and generators: where performance is tested across a spectrum of integrated power and temperature measurements
Refrigeration Center of Excellence
Within this team, the very latest HVAC+R technologies – including cascade and CO2 systems – are being worked on. In addition, research is also ongoing into alternate refrigerants including F-gases, hydrocarbons, and hydrofluoro-olefins (HFOs) focused on securing performance and energy efficiency.
Using the results, any number of real-world scenarios can be explored. This team is also active in the development and evaluation of sanitation technologies. These include the elimination of particles, micro-organisms, gases, and odors involved with passenger rail AC units – and the impact of door openings. Benefiting from these types of in-depth research, ETC is leading the way in developing new test methodologies – while also being a source of new patents (42 and counting!).
Reliability and analysis
Another core aspect of ETC is assessing the reliability of components and final products. Working in support of Thermo King’s product development function, the team here typically runs tests and analyses to determine:
- Reliability: predicting performance over time and in extreme conditions, to monitor wear and tear on items such as belts and bearings and define component service intervals
- Strength and stiffness: with analysis extended from thermal expansion and shape optimization to fatigue life prediction and aerodynamic pressure simulation
- Noise and vibration: where the goal is to optimize designs with respect to acoustic performance, and ensuring they don’t degrade beyond acceptable limits due to constant vibrational forces
- Material analysis: which analyzes advanced wear and friction down to the microscopic level
Testing center of excellence
Last but by no means least come ETC’s testing facilities. These are comprised of a series of unique labs that sport highly specialized equipment. These facilities ensure Thermo King products only reach the market after they’ve proven to withstand the toughest of conditions.
For example, ETC has a large-scale ‘shaking table’ to simulate several years of operation in just a few days. We can also simulate concerns such as sun damage, salt spray, air filtration efficiency, and acoustic fields. In a recent test, the ETC team even built a mock-up of a rail car to validate noise measurements in a ducting system!
Proceeding with confidence
ETC Prague is therefore a common destination for Thermo King customers. On an almost daily basis we have visitors in the climatic chambers (where for one of our latest examinations, a passenger rail car was tested at extreme conditions to measure airflow distribution and temperature), our vibration and corrosion labs, and many more besides.
As for what makes ETC stand out from other facilities, the list is long but includes the fact that it’s fully adapted for work on low GWP refrigerants – including A2L, CO2, and A3. These are advanced safety measures that extend to Li-ion battery testing to further boost our focus on green technologies.
All of this is fully supported by our impressive list of accreditations, including ISO9001, ISO17025, and IRIS certification as demanded by most rail manufacturers. It’s a complete package of skilled experts, innovative technology, and the latest environmental and safety standards – all aligned to our on-going customer commitments.
Other relevant articles that might interest you
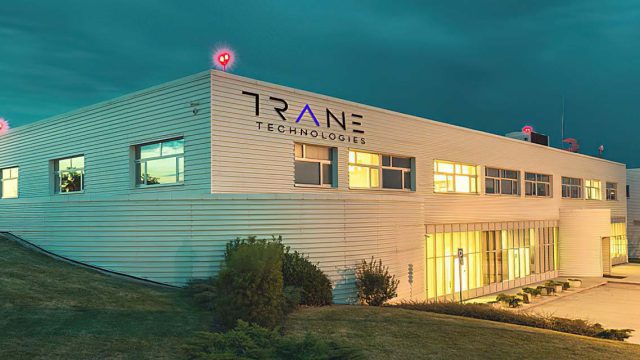
Rail
A tour of the ETC centre in Prague: a dedicated Thermo King testing lab.
Second only to aviation, the railway sector is one of the most regulated industries in public …
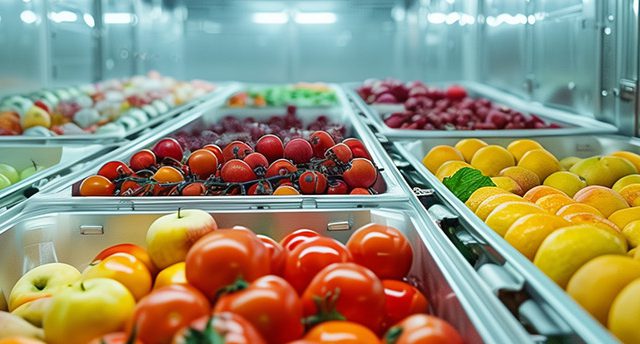
Marine
The science behind refrigeration: The difference a degree makes in container shipping.
Why tiny fluctuations in marine reefer temperatures can spoil cargo, and how to prevent them.