HVAC refrigerants in the rail sector: Assessing your options
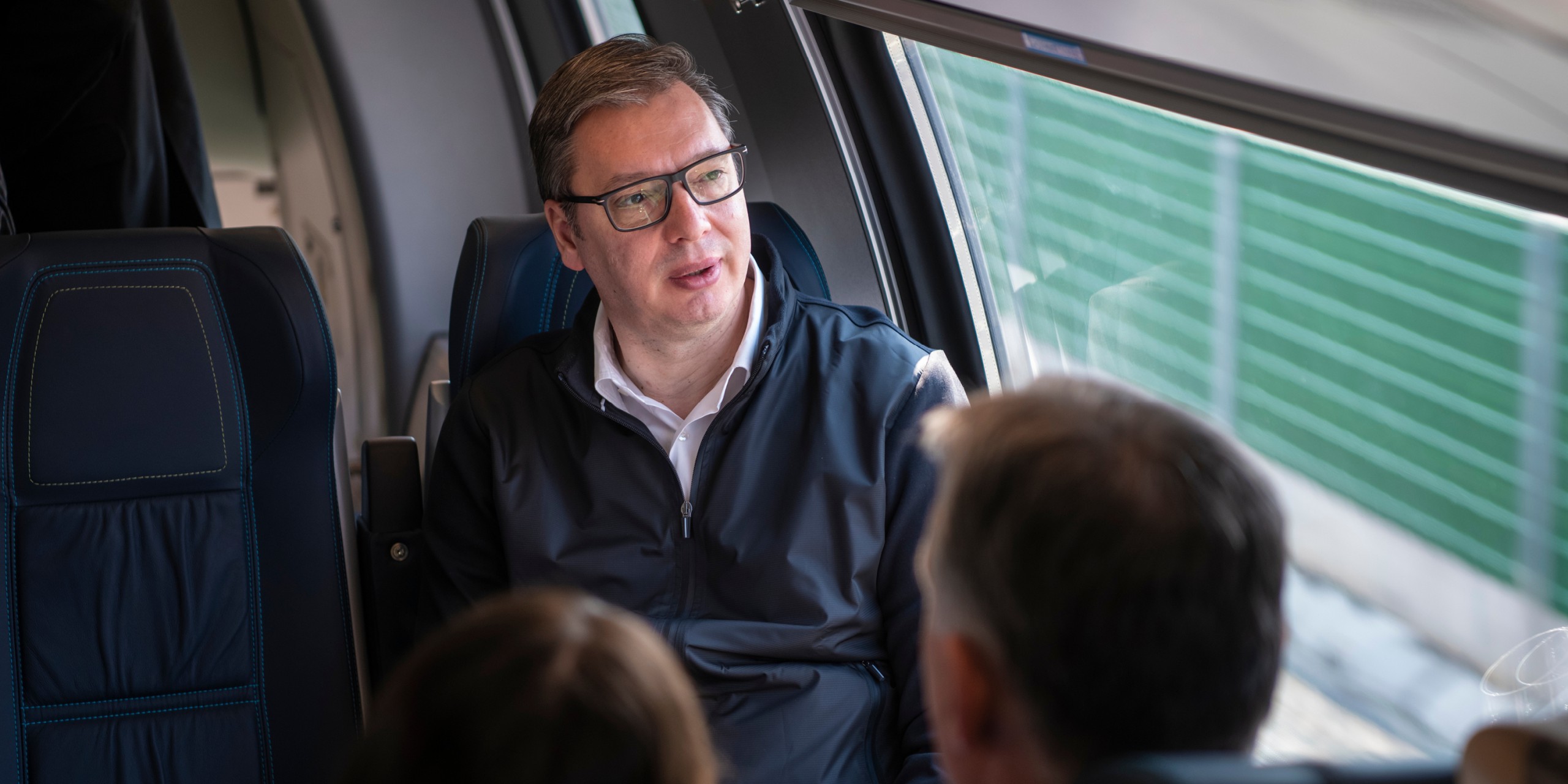
We all like to work and travel in comfort, no matter where in the world the commute takes place. Especially when it comes to traveling on public transport – whether via bus, tram or rail – which is increasing due to an ever-growing focus on sustainability. This is of course a good thing, with vehicles and locomotives that transition to electric emitting less and less emissions.
Alongside this growth in passenger numbers comes an increased emphasis on comfort during travel. Key here is the Heating, Ventilation, and Air Conditioning (HVAC) unit, and in particular the type of refrigerant being used. A choice that ultimately comes down to one between nature versus innovation as environmental demands shape long-term investment strategies.
It’s an interesting decision for rail operating companies, and one that’s set against the backdrop of four distinct generations of refrigerant development – each of which is defined by specific technological advancements:
· First Generation (1830s – 1930s): This era essentially used what worked and was available, including natural refrigerants like ammonia, carbon dioxide, and sulfur dioxide. They were effective but often highly toxic or flammable
· Second Generation (1930s – 1990s): Saw the development of chlorofluorocarbons (CFCs) and hydrochlorofluorocarbons (HCFCs). Refrigerants that were non-toxic and non-flammable but were found to deplete the ozone layer
· Third Generation (1990s – 2010s): Where Hydrofluorocarbons (HFCs) replaced CFCs and HCFCs. HFCs were far more ‘ozone friendly’, but this value was negated by a high global warming potential (GWP)
· Fourth Generation (2010s – Present): The latest generation which is focused on achieving both low-GWP and greater efficiency, with refrigerants such as hydrofluoroolefins (HFOs) and natural refrigerants like carbon dioxide and propane.
The choice for rail operators
The fact that a lack of consensus or standardization exists for HVAC refrigerants is evidence that no ideal option currently exists. Hence the choice between nature versus innovation, which poses two distinct questions:
· Should the rail industry ‘return to basics’ and accept natural refrigerants, despite their disadvantages (high flammability, low efficiency, high pressure etc.)?
· Or is it better to invest in synthetic refrigerants, hoping for another step change in chemistry that helps usher in a more sustainable fifth generation?
Above all, any tradeoffs for HVAC equipment (i.e. heat pumps and accessories that provide a comfortable environment for passengers and staff across all 4 seasons), must accommodate refrigerants that are energy efficient, safe, and sustainable – while being attractive in terms of overall equipment investment and lifetime operating costs.
Synthetic refrigerants
For any man-made synthetic option, one of the biggest hurdles to navigate is regulation. This is especially the case in Europe, where efforts to slow down climate change have led to the latest rendition of the F-Gases (fluorinated gases) regulations. Aligned to the EU’s Green Deal, the legislation looks to eliminate the use of today’s most frequently employed HFCs by 2050.
In response, the wider chemical industry is striving hard to develop new refrigerants that offer a GWP of around 1 – meaning they’re only trapping the same amount of heat in the atmosphere as say a natural gas like CO2.
Yet further obstacles exist. For example, research continues to place the focus on:
· PFAS (Per- and Polyflouroalkyl substances) that are used in various refrigerants and are known for their persistence in the environment and potential health impacts
· TFAs (triflouroacetic acid) which is a byproduct that can form from the atmospheric breakdown of certain refrigerants such as HFCs and HFOs
Natural refrigerants
As for the development of natural refrigerants, the two leading contenders are propane (R-290) and CO2 (R-744). These however also bring their own unique challenges:
· Propane: due to its high flammability, propane represents for rail operators a safety risk if not handled correctly. This impacts usage, handling, and storage, requiring investment in infrastructure to ensure adequate ventilation in workshops – and in train design to eradicate both leakage opportunities and sources of ignition
· CO2: which although non-flammable (therefore requiring less safety measures) is not as energy efficient as propane, particularly in warmer climates which serve to drive up operating costs (power consumption in cooling mode). In addition, CO2 systems operate at much higher pressure compared to other refrigerants. This overall result is a demand for specialized, more complex equipment to maintain cooling efficiency on trains (larger inverters for example), which in turn can limit overall scalability
The good news is that natural refrigerants are environmentally friendly and offer a low GWP rating, which helps explain their growing popularity. Yet due to the drawbacks listed above one could propose the choice of refrigerant as being roughly determined by moderate and cold climates (CO2) and warm climates (propane). A fact that’s primarily due to ambient temperatures, and how higher these are above the 35°Celsius mark when cooling typically kicks in, which is where the inefficiency of CO2 becomes increasingly pronounced.
HVAC flexibility
For the rail sector, choice of refrigerant brings opportunities in terms of optimizing the equipment for each specific application – but also unwanted complexity. Equally, a lack of standardization on a global level, and differences in legislation as well as in refrigerant availability also impacts the suppliers of the HVAC units themselves.
At Thermo King our temperature control technologies are used by rail customers across the globe to meet their performance, cost, and sustainability objectives. At the same time, we’re also a company committed to sustainable development. As a result, our HVAC units are designed and tested to be refrigerant agnostic, and able to run on all the common options currently available, including CO2 and propane.
This we do to help protect our customers’ long-term resilience, while also enhancing their day-to-day agility in the face of evolving opportunities.
Explore every opportunity for a sustainable and cost-effective future
With currently no ‘one size fits all’ HVAC refrigerant for the rail sector, it pays to invest in technology that helps keep your options open. At Thermo King our units represent the ideal mix of performance and flexibility to help you maximize today, while being ready for whatever happens tomorrow.
To find out more about our HVAC units for rail, click here.
Other relevant articles that might interest you
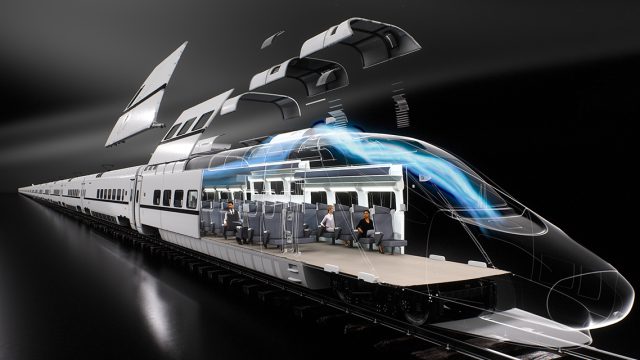
Rail
The future of Thermo King Rail HVAC.
As inner cities and highways become ever more traffic-clogged, the demand for safe, sustainable modes of …
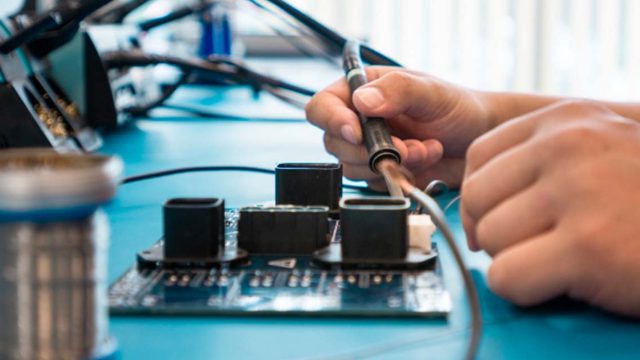
Rail
Putting innovation to the test: Thermo King’s Engineering and Technology Center.
The world of transport temperature control never stands still. It’s an industry defined by innovation, …